Model Based Systems Engineering is a critical aspect of the 21st century as systems become more and more complex. And that’s the journey, to continue to move it forward to deal with even more complexity in a better way. As the products are getting increasingly complex, the connections between components have become more and more important. The connections can be physical or functional. For a simple system, it is easy to see how adding individual subsystems creates more and more potential connections. Each of these connections are opportunities for waste, errors, and rework that can result in projects that are late, over budget, and have reduced capabilities in terms of performance, maintenance, and future upgrade ability. The practice of systems engineering has evolved to mitigate the risk associated with complex system development. It focuses on defining customer needs and necessary functionalities primarily in the product development cycle. Considering the complete problem definition documentation then continuing with synthesis of design and system validation. Ideation, Operations, schedule and cost, performance, training and support, test, manufacturing and disposal.
What is Systems Engineering?
Systems engineering is a mindset that results in an interdisciplinary perspective deals with management and design of complex systems through the product life cycles. It was actually an effort to close the gap between systems and software engineering. As systems had more and more software content, communication gap was beginning to impair system development and system performance. In those early days, it was all about closing the system software gap. From the year 2007 onward, INCOSE, the International Council on Systems Engineering, has progressively invested more time and more energy to move the community forward. What we see now is model-based systems engineering is much bigger. It’s not about the software component, it’s about the systems engineering component on all fronts. And perhaps the biggest change is model-based systems engineering is now becoming the linchpin to, it can be called model-based engineering, digital thread, digital tapestry, but really connecting to digital engineering so that we can better deliver capabilities to these complex problems we face.
Model Based:
A key component of model-based systems engineering is the model-based definition, or MBD. Model-based definition embodies the concept of moving away from paper-based documentation and drawings to digital, 3D CAD representation, manufacturing data, and performance models.
Model-Based Systems Engineering:
According to INCOSE, model-based systems engineering, also known as MBSE, is the formalized utilization of modelling to supporting system necessities, structure, investigation, verification, and validation activities starting from conceptualization to disposal through the product life cycle. Model-based systems engineering is still in a nascent stage of development and is an immense topic to be fully addressed. This concept is offering a broad perspective with connections throughout the industries that will give the opportunity to learn and work more. Now, Model-Based Systems Engineering sounds like a technology and a technical problem – it’s not. It’s an organizational change initiative because it’s all about how you represent knowledge.
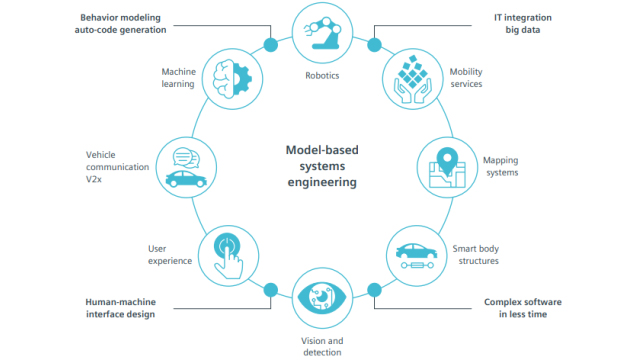
Image Credit: plm.automation.siemens.com
Implementations of MBSE:
The model today as we represent it in a higher fidelity way, is represented digitally. It is more accessible to everybody else in the program, and by making it more accessible, increase in alignment, increase understanding, and most importantly, increase shared understanding as requirements change, as needs change, as technologies change.
The quantity of information accumulates throughout the lifecycle into a large amount of raw data that can be used to describe the life of a product. The digital thread describes the electronic files and the data pathways that enable the re-purposing, reuse and traceability of information in the development, definition, production and support of a part or system throughout its life. The thread weaves through connected machines, factories and supply chains to enable data aggregation, analysis and action, forming a digital quilt or digital tapestry that encompasses an entire product or system. The digital thread connects conceptual design requirements, analysis, detailed design, manufacturing, inspection, operations, refit and retirement. As a result, a finished assembly can be traced back to the original requirements and design model.
A Model-Based Enterprise (MBE) has clear benefits. However, it might seem daunting to implement. MBE seems very idealistic, and for a small business, the idea of a Model-Based Enterprise might seem like an unnecessary investment. However, studies have shown that small businesses can achieve MBE without a significant investment. Better if it would be to think about a road map as a pathway, rather than a dramatic step change. So, Model-Based Systems Engineering, just like systems engineering itself, is intended to be scalable and tailorable, and there is no one size fits all. Model-Based Systems Engineering, like systems engineering, should begin with the exact purpose and it’s a business value. Are you after quality? Are you after responsiveness? After agility? After innovation? Whatever you pick, it helps to define the implementation of Model-Based Systems Engineering.