Technology is evolving faster than ever before and it’s having a huge impact on manufacturing. Fifteen years ago the products saw a three to five-year time to obsolescence, compared to perhaps 14 to 18 months today. What does this mean to manufacturers? They need to reimagine how they take a product from ideation to a useable product into consumer’s hands, and the product needs to have incredible levels of customization, quality and performance along with the competitive price. The fact of the matter is, with the improvements made in information technology, material sciences, production technologies and supply chain strategies for the past 50 years, we’re well positioned to challenge the traditional way products are developed. We are at the initial stages of a new era and the next Industrial revolution popularly termed as Industry 4.0. In this era, we will develop products virtually, bypassing time-consuming and non-value added task associated with traditional methods.
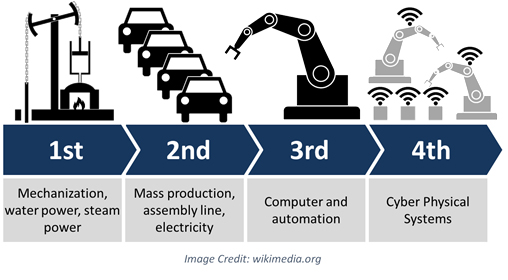
Mechanization and of the machinery and production systems are the aims of the First industrial revolution utilizing water and steam power around in 1780. In 1870 the Second revolution of industries hits the market with the help of electricity results large scale manufacturing. The 3rd revolutions comes with automation of production processes utilizing electronics and information technology in 1969. Presently a 4th Industrial Revolution is escalating on the Third, has been happening since the middle of the last century by digital transformation. It is characterized by a blending of technologies that is obscuring the lines between the digital, physical, and biological spheres.
We are now entering what is being described as a fourth revolution, also known as Industry 4.0. It is the next phase in the evolution of manufacturing. Combining the cyber capabilities resulting from advances in computing with physical systems to create a highly intelligent, interactive, and automated manufacturing ecosystem. That integrates product design, manufacturing, and logistics.
Effectively, artificial intelligence is surrounding us, from self-driving vehicles and automatons to drones to virtual assistants and programming that interpret or contribute. Noteworthy advancement has been made in AI as of late, determined by exponential increments in figuring power and by the accessibility of tremendous amount of information, from programming used to find new medications to algorithms used to foresee our cultural interests. Day by day Digital manufacturing technologies, in the interim, are cooperating with the biological field. Designers, Engineers, and architects are joining additive manufacturing, computational design, materials innovation, and to pioneer a symbiosis between microorganisms by the help of synthetic biology, our bodies, the items we devour, and even the buildings we reside in.
The Society of Automotive Engineers estimates that 90 percent of all products will be developed virtually in the coming years. So, how does this new product development process look? You have an idea, you convert the idea into a product and process model, which is virtually tested to make sure it meets customer requirements, and then, great! You go into production. It’s as simple as that. This is made possible by sharing data and information across all stages of the product life cycle, what is referred to as, the digital thread.
Manufacturing is the most tangible part of the product lifecycle because it results in a clear outcome. There are multiple definitions of the product lifecycle. Most differing only in their terminology or details. Lifecycle as all aspects of a product’s life, from its design through manufacture, deployment and maintenance. Culminating in the product’s removal from service and final disposal. The first stage in a product’s lifecycle is planning. In a product’s lifecycle, many iterations may be required before customer approval is received. In traditional paper based processes, information sharing can consume valuable time and delay the development process. In traditional processes, there is also a lag during and in-between stages in the lifecycle as necessary approvals are sought. Sometimes, this can even result in losing first-to-market competitive advantage.
The Digital Manufacturing and Design Innovation Institute, defines digital manufacturing as an integrated set of tools that work with data sets for product definition having provision of tool design, design of manufacturing process, conceptualization, modeling and simulation, analysis of data, and further analyses necessary to optimize the processes of manufacturing. Deployed throughout the product lifecycle, digital manufacturing enables more quickly and authoritatively share information in the design process. With all the data generated in every part of the lifecycle representing a digital thread. This digital thread can be used to create a computer based digital twin. An integrated system of data, models, and analyses that can be used in design, manufacturing, support, and disposal. These concepts all come together as the Fourth Industrial Revolution, Industry 4.0.
An example of the vision and promise of Industry 4.0 can be found in the wind power industry. Wind power is an important component of the clean energy industry. An ongoing challenge for wind farm operators is the significant wear and tear of gearboxes. Gearboxes are expensive to fix especially after failure. However, if sensors on the turbine are linked with weather information and computational models, a very accurate simulation can be developed for each individual turbine. Enabling evidence based decision-making and the creation of predictive models for performance of individual turbines and the wind farm as a whole. This concludes the effectiveness of digital manufacturing and design.
Visited 1710 times, 1 Visit today